Injection Mold Tooling
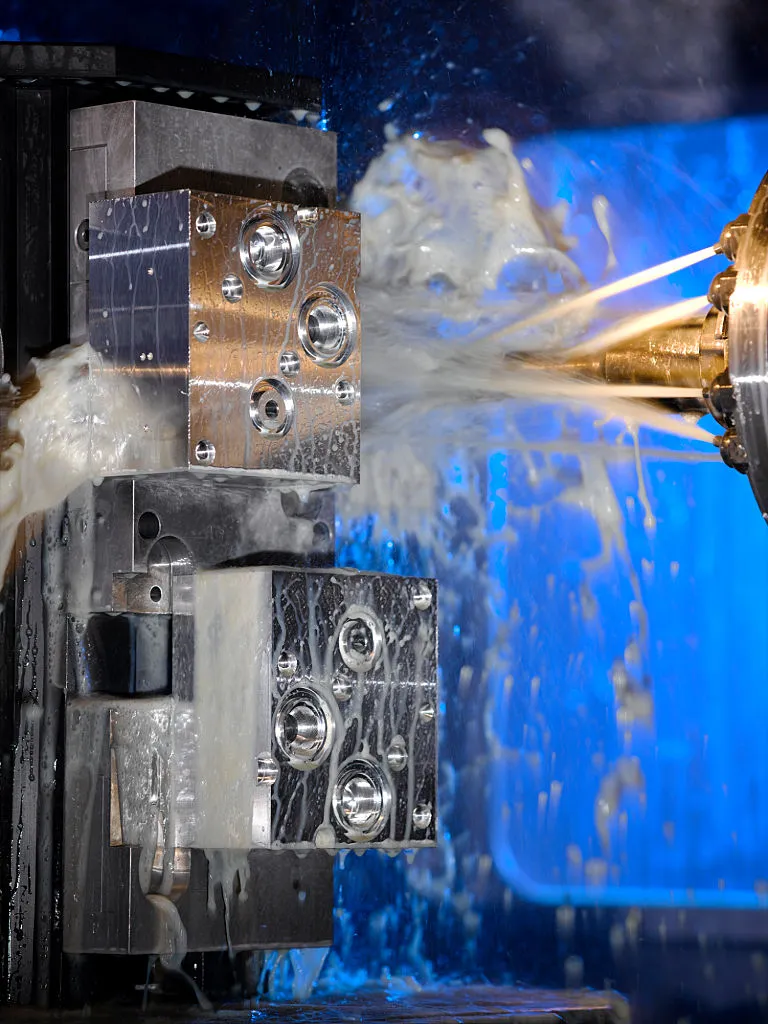
What is
Injection Mold Tooling?
Injection mold tooling refers to the specialized tools used to shape and form plastic materials into precise, complex components. This process is crucial for ensuring the consistency and quality of mass-produced parts. YG specializes in creating bespoke mold designs and manufacturing solutions tailored to meet the unique requirements of your products, ensuring high-quality and consistent results across production runs.
Our versatile approach allows us to develop both prototype and production molds at competitive prices. With rapid lead times, we streamline your production process, accelerating your product’s journey to market. Ready to enhance your plastic part production? YG is here to support you every step of the way.
YG Mold Tooling Services
YG offers comprehensive mold tooling services designed to meet the diverse needs of our clients. Whether you require rapid prototyping or high-volume production, our skilled team and advanced technologies ensure precision and efficiency in every project.
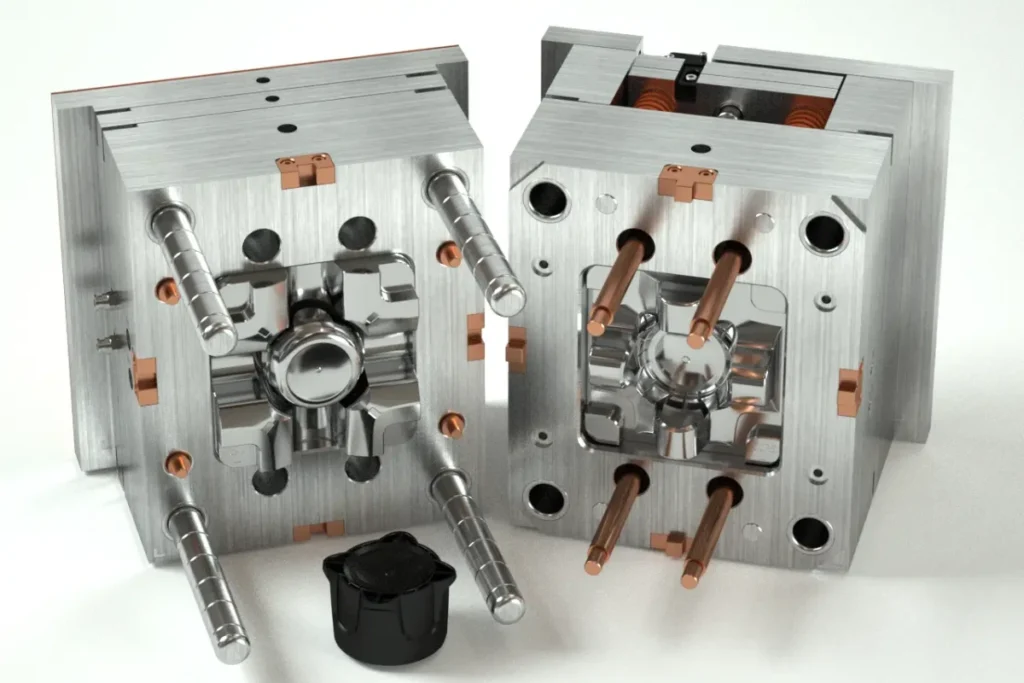
Rapid Mold Tooling
Our rapid mold tooling service is designed for quick turnaround times, enabling you to validate designs and accelerate product development. We use advanced techniques to produce high-precision molds swiftly, ideal for prototyping and short-run production.
Production Mold Tooling
For long-term production needs, we focus on creating molds that withstand high-volume manufacturing while maintaining consistent quality. Our tooling solutions are optimized for efficiency and longevity, ensuring reliable performance over time.
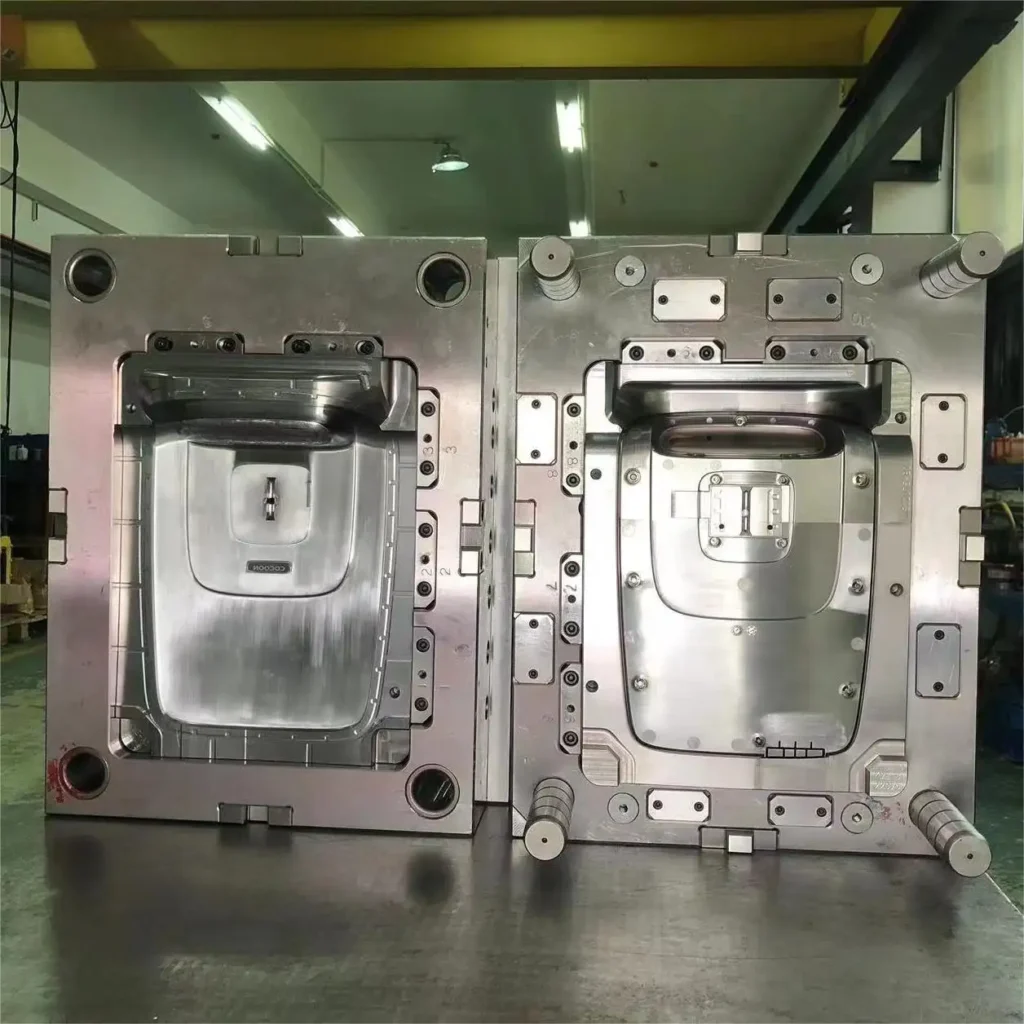
Advantages of YG Custom Injection Molds
Discover the distinct advantages that set our custom injection molds apart. From expert engineering teams and cutting-edge manufacturing equipment to our commitment to quality and innovation, we provide tailored solutions that enhance efficiency and performance for every project. Explore how our comprehensive approach ensures exceptional results and customer satisfaction.
Expert Engineering Team
Our team consists of 80+ skilled mold manufacturing engineers who bring extensive industry experience and technical expertise to the table. They are committed to delivering innovative solutions tailored to each project, ensuring we consistently meet and exceed customer expectations through their dedication and creativity.
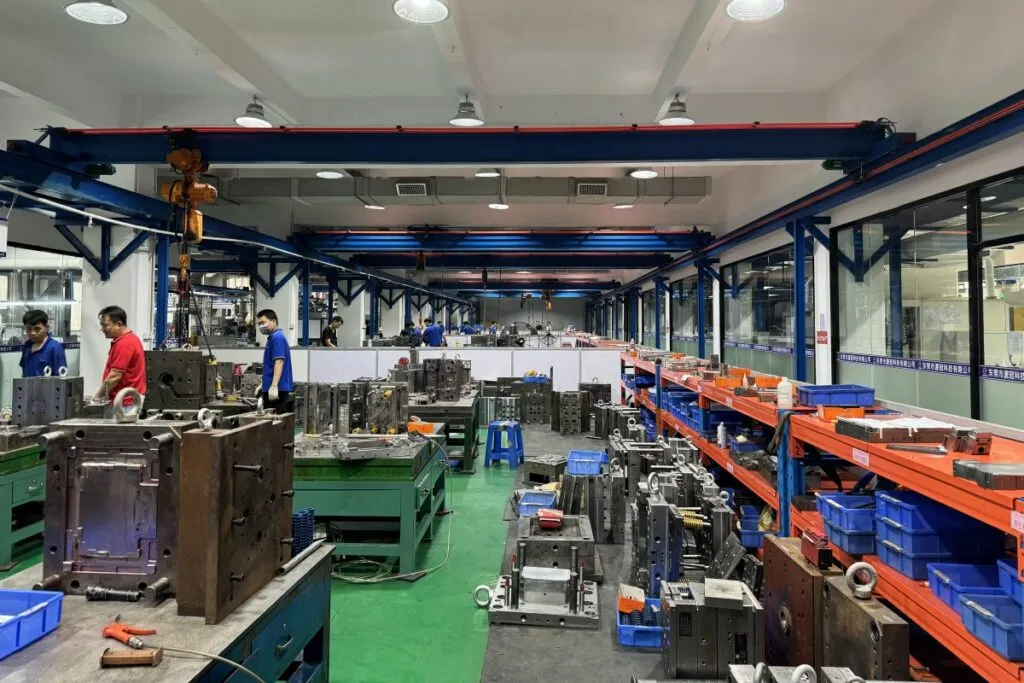
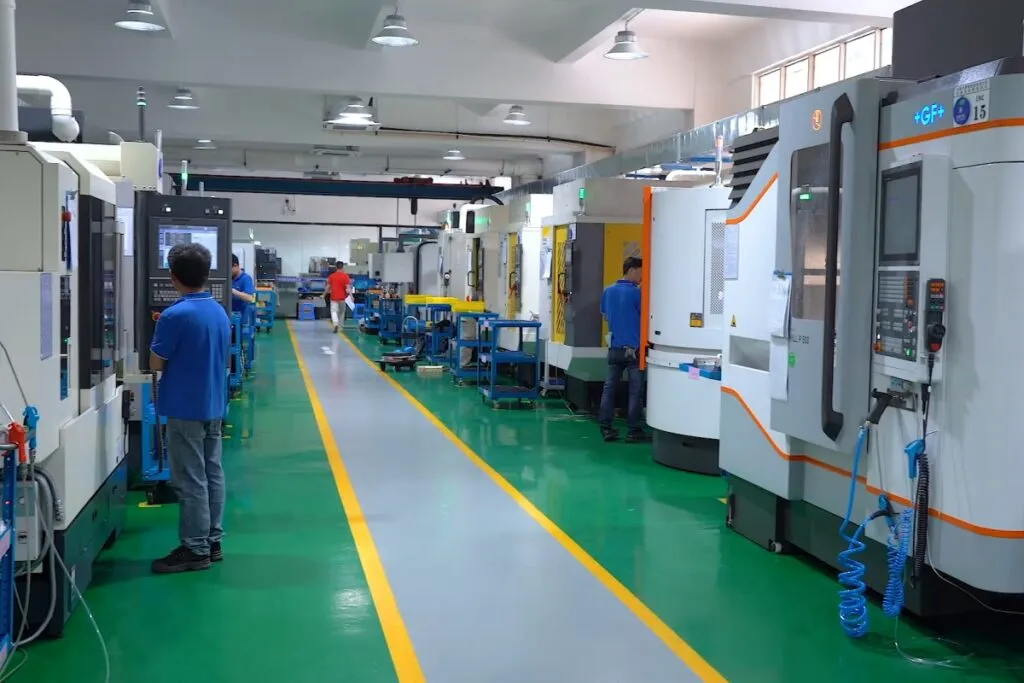
Advanced Manufacturing Equipment
Our facility houses 100+ cutting-edge CNC machines from renowned brands, including CNC drilling machines, EDM machines, wire-cut machines, and coordinate measuring machines. This state-of-the-art equipment guarantees high precision and efficiency in mold manufacturing, enabling us to tackle complex designs and large-scale production with ease and reliability.
Design Optimization Capability
We utilize a suite of advanced design software, such as Pro-E, UG, Auto CAD, and Solidworks. These powerful tools allow our design team to conduct thorough design optimizations and simulations, ensuring that our molds deliver optimal performance and manufacturing efficiency, tailored to meet the specific needs of each project.
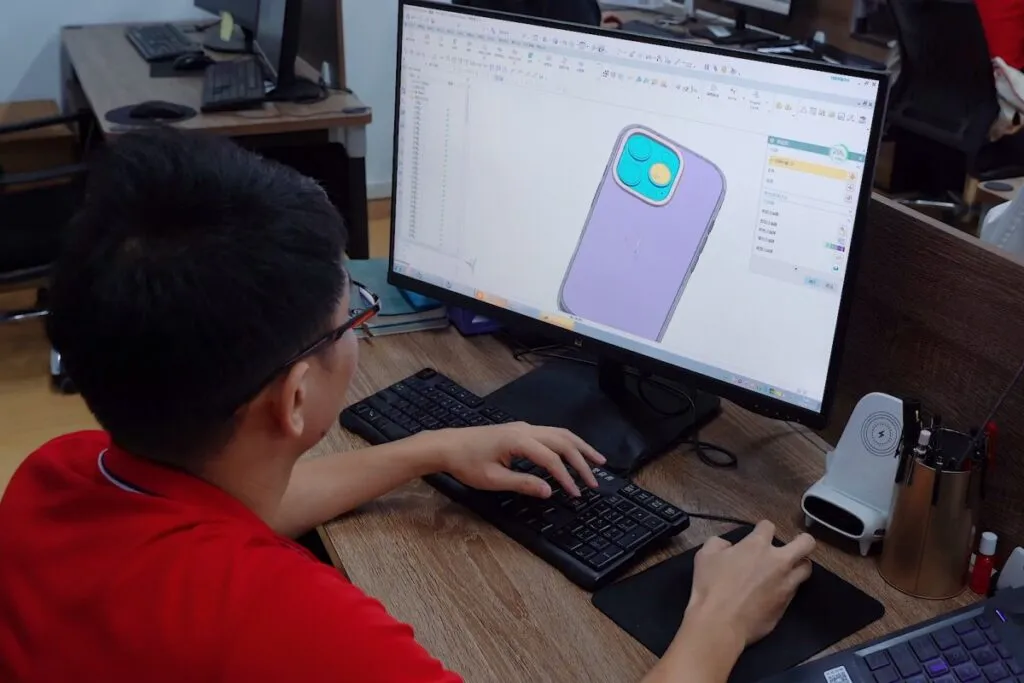
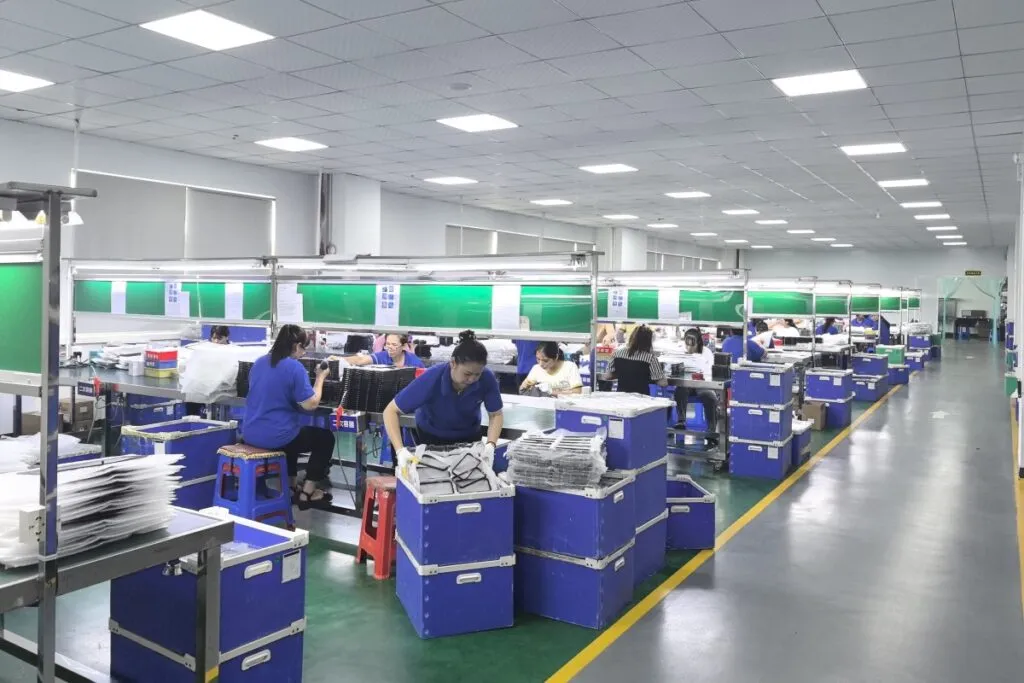
Rigorous Quality Control
In strict adherence to ISO standards, we have established a comprehensive quality management system. Our team of 53 quality managers oversees IQC, IPQC, FQC, and OQC processes, ensuring that every product meets the highest standards. With advanced testing equipment, we maintain defect rates well below industry averages, issuing detailed quality reports and retaining samples for traceability.
Why Choose Us
Choosing YG for your injection mold tooling needs means partnering with a leader in precision manufacturing. We offer:
Comprehensive Solutions
From design to delivery, we handle every aspect of mold production.
Customer-Centric Approach
Tailored solutions and responsive support to meet your unique requirements.
Innovative Technology
Utilizing the latest in manufacturing technology to ensure superior results.
Proven Track Record
Successful projects across various industries showcase our reliability.
Main Types of Injection Molds
We offer a variety of injection mold types to suit different manufacturing requirements

Single Cavity Molds
Our expertise and reliability are evidenced by a track record of successful projects spanning multiple industries.

Multi-Cavity Molds
Increase production efficiency by producing multiple parts simultaneously.

Family Molds
Manufacture different parts of an assembly in one cycle, reducing costs and time.

Insert Molds
Incorporate metal or other materials within plastic parts for enhanced functionality.
Process of Injection Mold Tooling
The injection mold tooling process is a comprehensive sequence of steps designed to create high-precision molds that meet specific manufacturing needs. At YG, we follow a meticulous approach to ensure the highest quality and efficiency:
1. Initial Consultation and Design
The process begins with an in-depth consultation to understand the client’s specific requirements and objectives. Our experienced engineers collaborate with you to develop a detailed mold design, utilizing advanced CAD software to create precise 3D models. This stage is crucial for identifying potential design challenges and optimizing the mold for manufacturability.
2. Material Selection
Based on the design and intended production volume, we select the appropriate materials for the mold. Factors such as strength, thermal conductivity, and cost-effectiveness are considered to ensure optimal performance and longevity of the mold.
3. Prototype Development
For complex designs or new products, we often create a prototype mold to validate the design and functionality. This allows for testing and refinement before committing to full-scale production tooling, reducing risk and ensuring the final product meets all specifications.
4. Tool Fabrication
Utilizing state-of-the-art CNC machining, EDM, and other precision manufacturing technologies, we fabricate the mold components with exacting accuracy. Our skilled technicians ensure that every detail is executed to perfection, adhering to the highest quality standards.
5. Assembly and Testing
Once the individual components are manufactured, they are carefully assembled and tested. We conduct rigorous quality assurance checks to verify that the mold functions correctly and produces parts that meet the desired specifications.
6. Production and Optimization
With the mold fully assembled and tested, it is ready for production. We continuously monitor performance and make any necessary adjustments to optimize efficiency and quality, ensuring a smooth and reliable manufacturing process.
7. Maintenance and Support
Post-production, we offer comprehensive maintenance and support services to extend the life of your mold and ensure consistent performance. Regular maintenance helps prevent wear and tear, minimizing downtime and maximizing productivity.
Materials for Injection Mold
Choosing the right material is essential for mold performance and durability. We offer a range of materials, including:

Steel (P20, H13)
Renowned for its exceptional strength and durability, making it an excellent choice for high-volume production where wear resistance is crucial.

Aluminum
Valued for its lightweight nature and cost-effectiveness, it is particularly well-suited for prototyping and smaller production runs, offering flexibility and ease of use.

Beryllium-Copper Alloys
Known for their superior thermal conductivity, these alloys help significantly reduce cycle times, enhancing efficiency in the production process.
Get Your Custom Mold
Ready to enhance your manufacturing process with precision custom injection molds? Contact us today to discuss your project and receive a tailored quote.